Ensuring Quality in Manufacturing: Best Practices from the Experts
Understanding the Importance of Quality in Manufacturing
Quality is the cornerstone of manufacturing success. It ensures customer satisfaction, reduces costs, and enhances the reputation of a company. In a competitive market, maintaining high standards of quality can be a differentiator that sets a business apart from its competitors. By prioritizing quality, manufacturers can build trust with consumers and foster long-term relationships.

Implementing a Robust Quality Management System (QMS)
A Quality Management System (QMS) is essential for ensuring consistent quality across all manufacturing processes. A well-designed QMS includes policies, procedures, and responsibilities that guide employees in achieving quality objectives. It also involves continuous monitoring and improvement to adapt to changing market demands and technological advancements.
Key components of a successful QMS include:
- Clear documentation of processes and procedures.
- Regular audits to assess compliance and effectiveness.
- Employee training to ensure understanding and adherence to quality standards.
Leveraging Technology for Enhanced Quality Assurance
The integration of technology in manufacturing processes has revolutionized quality assurance. Advanced tools such as automated inspection systems, data analytics, and machine learning algorithms provide real-time insights into product quality. By leveraging these technologies, manufacturers can detect defects early, minimize waste, and optimize production efficiency.
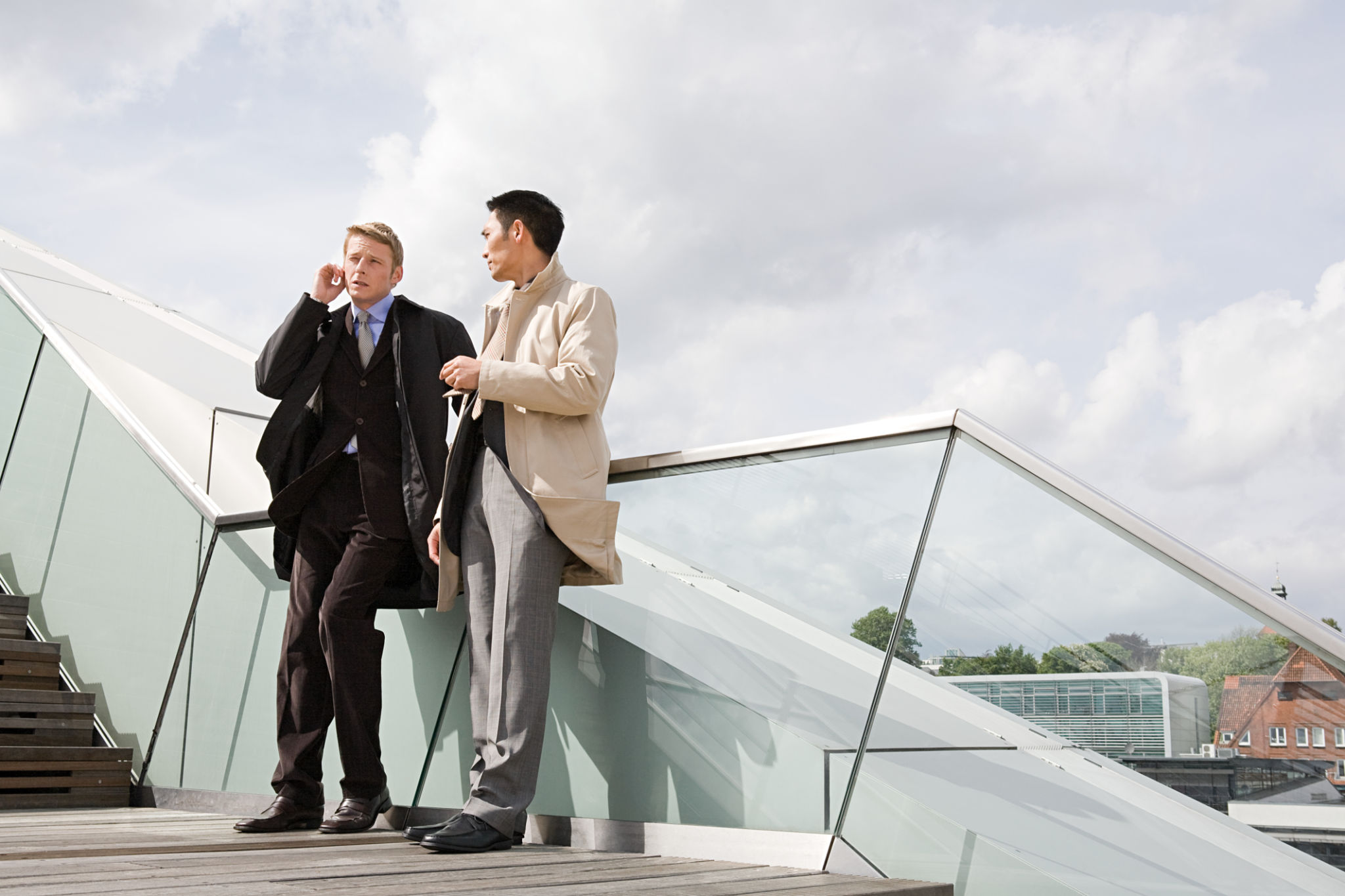
Automation plays a crucial role in reducing human error and increasing precision. For instance, automated inspection systems can perform non-destructive testing with greater accuracy than manual methods. Additionally, data analytics can identify patterns and trends that help in predicting potential quality issues before they occur.
Fostering a Culture of Continuous Improvement
A culture of continuous improvement is vital for maintaining high-quality standards. This involves encouraging employees at all levels to contribute ideas for process enhancements and recognizing their efforts. Implementing practices such as Kaizen or Six Sigma provides structured approaches for identifying inefficiencies and implementing corrective actions.
Regular feedback loops and open communication channels are essential to ensure that improvements are sustainable. By fostering a culture where quality is everyone's responsibility, manufacturers can drive innovation and maintain competitive advantage.

Collaborating with Suppliers for Quality Assurance
Supplier quality management is another critical aspect of ensuring overall product quality. Manufacturers should collaborate closely with suppliers to set clear expectations, conduct regular assessments, and provide feedback on performance. Building strong relationships with suppliers helps in obtaining high-quality raw materials and components, which are fundamental to the production process.
Joint development programs and shared quality objectives can lead to better alignment and mutual benefits. By working together, manufacturers and suppliers can enhance efficiency, reduce costs, and improve product quality.
Adapting to Regulatory Standards and Compliance
Compliance with industry regulations and standards is non-negotiable in manufacturing. Staying up-to-date with regulatory requirements ensures that products meet safety and quality benchmarks. Manufacturers must implement robust compliance management systems to monitor changes in regulations and adapt processes accordingly.
Regular training sessions and updates for employees help ensure that everyone is aware of current regulations and understands their role in maintaining compliance. By prioritizing regulatory adherence, companies can avoid costly penalties and maintain their reputation for quality.