Comparing Quality Management Tools: What Works Best for Your Business?
Introduction to Quality Management Tools
In today's competitive business landscape, maintaining high standards of quality is paramount. Quality management tools are essential for ensuring that products and services meet customer expectations and regulatory requirements. However, with a plethora of options available, selecting the right tool for your business can be daunting. This blog post aims to compare different quality management tools to help you make an informed decision.
Understanding the Basics
Quality management tools are software applications designed to streamline processes, enhance efficiency, and maintain quality standards. They often include features like document control, audit management, non-conformance tracking, and corrective action management. The ultimate goal is to ensure continuous improvement and customer satisfaction.
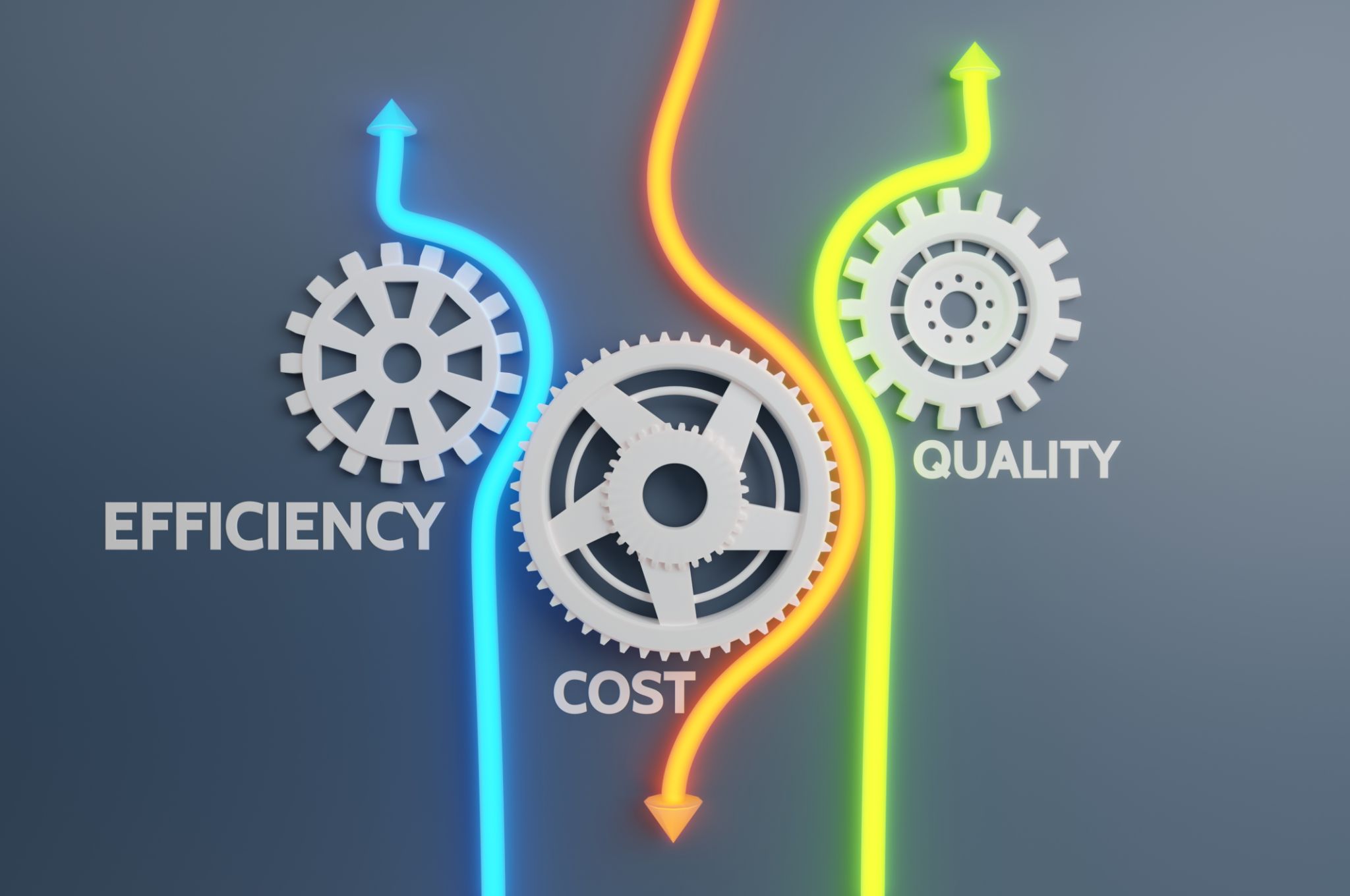
Popular Quality Management Tools
Several tools have gained popularity in the market due to their robust features and user-friendly interfaces. Some of the most widely used quality management tools include:
- ISO 9001: A globally recognized standard that provides guidelines for quality management systems.
- Six Sigma: A methodology focused on process improvement and reducing defects.
- Total Quality Management (TQM): An approach that involves all members of an organization in improving processes and products.
- Lean: A systematic method for waste minimization within a manufacturing system.
Factors to Consider When Choosing a Tool
When selecting a quality management tool, businesses should consider several factors to ensure they choose a solution that aligns with their needs. Key considerations include:
- Scalability: Will the tool grow with your business?
- Integration: Can it seamlessly integrate with existing systems?
- User-Friendliness: Is the interface intuitive for users?
- Cost: Does it fit within your budget constraints?
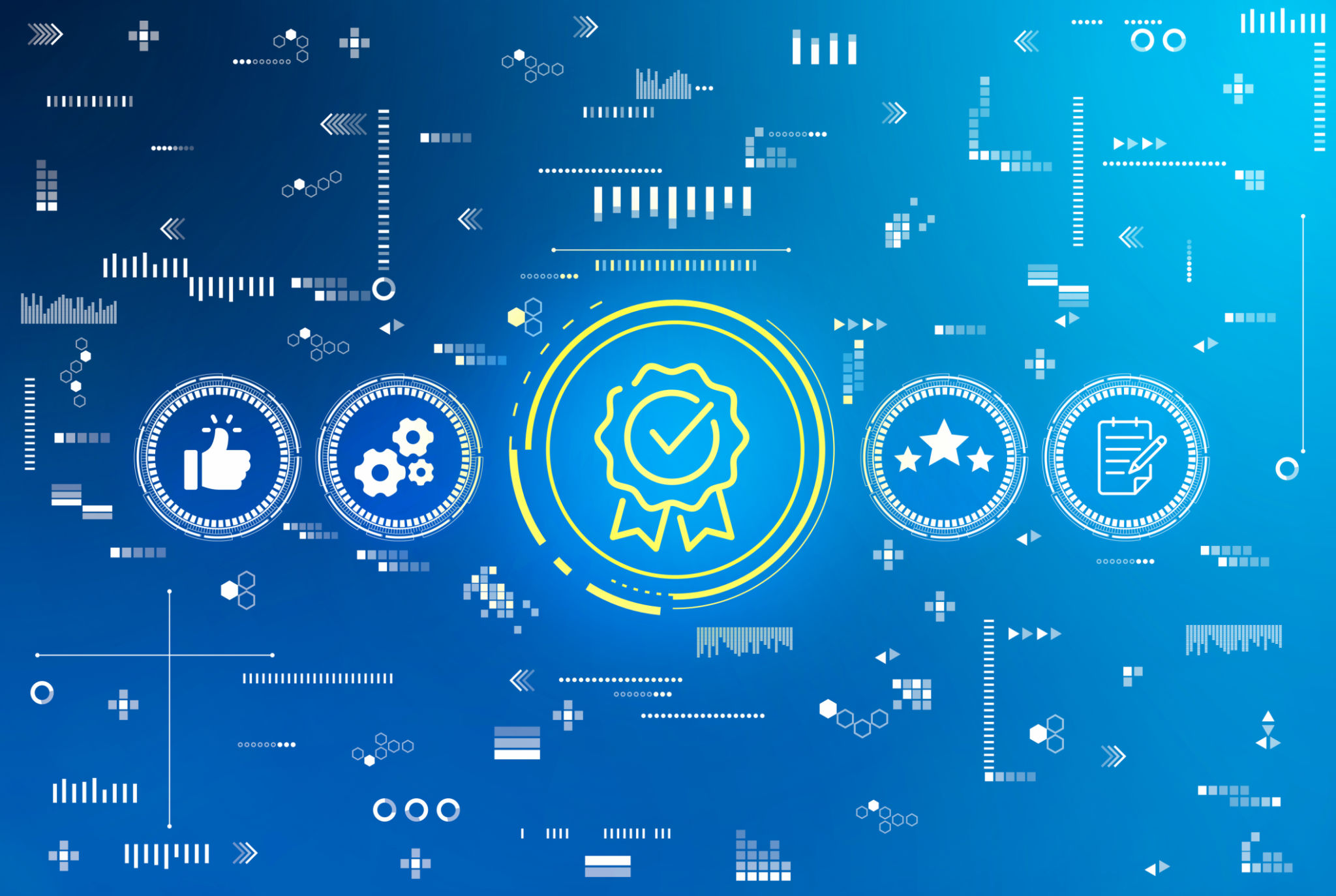
Comparing Key Features
Each quality management tool offers distinct features that cater to different business needs. For instance, ISO 9001 provides a comprehensive framework for managing quality assurance, while Six Sigma focuses on statistical analysis to reduce variability. TQM emphasizes a company-wide approach, promoting a culture of continuous improvement. Lean, on the other hand, prioritizes efficiency and waste reduction.
Customization and Flexibility
Another crucial aspect to consider is the customization and flexibility offered by the tool. Businesses should assess whether the tool can be tailored to their specific industry requirements and processes. A flexible tool allows for modifications as business needs evolve over time.

Implementation and Support
The implementation process can significantly impact the success of a quality management tool. Look for solutions that offer comprehensive support during the setup phase, including training resources and customer service. Ongoing support is equally important to address any issues that may arise post-implementation.
Conclusion: Making the Right Choice
Choosing the right quality management tool is a strategic decision that can enhance operational efficiency and product quality. By considering factors like scalability, integration, cost, and customization, businesses can find a solution that meets their unique requirements. Ultimately, the right tool will foster a culture of excellence and drive continuous improvement across the organization.